The implementation of the new national standard has made green upgrading of the sheet metal industry a general trend
The implementation of the new national standard has made the green upgrade of the board industry an inevitable trend
Against the backdrop of growing market demand and increasingly tight wood resources, my country's wood-based panel industry has developed rapidly. Data show that my country, with only 4.7% of forest resources, produces more than 36% of the world's wood-based panel products, and has become a major producer and trader of wood-based panels. In 2016, the national output of wood-based panels exceeded 300 million cubic meters, with an output value of about 650 billion yuan, an increase of 7.4% over the previous year. Except for Tibet, Qinghai, Beijing and Taiwan, 28 provinces (autonomous regions and municipalities) in China have wood-based panel production, of which Shandong, Jiangsu, Guangxi, Anhui, Henan, Hebei and Guangdong have an annual output of more than 10 million cubic meters.
However, although my country's wood-based panel industry has achieved remarkable development, existing problems and drawbacks have gradually emerged. Substandard wood-based panel products have been repeatedly exposed, and one of the important factors is the excessive formaldehyde emission. It is understood that in the production process of wood-based panels, wood-based panel adhesives are the main source of formaldehyde release. In order to enhance the durability and strength of the panels, manufacturers usually need to add moisture-proof agents and adhesives to the production raw materials, so the manufacturing process and use environment of wood-based panels also have a significant impact on formaldehyde release.
Since May 1 this year, the new standard "Limit of Formaldehyde Emission from Artificial Boards and Their Products for Indoor Decoration and Renovation Materials" (GB 18580-2017) has been officially implemented. The new national standard has revised the formaldehyde emission limit value, stipulating that the formaldehyde emission limit value from artificial boards and their products for indoor decoration and renovation materials is 0.124 mg per cubic meter, and the limit mark is E1, canceling the E2 level of the original standard.
Under the requirements of the new standard, the green development and transformation and upgrading of the board industry is the general trend. Enterprises are facing more stringent environmental protection standards. How to reduce the formaldehyde content of artificial boards and their products, improve and improve production processes and production technologies, and provide consumers with healthy and safe products is the basis for the survival of enterprises and the way to compete and develop.
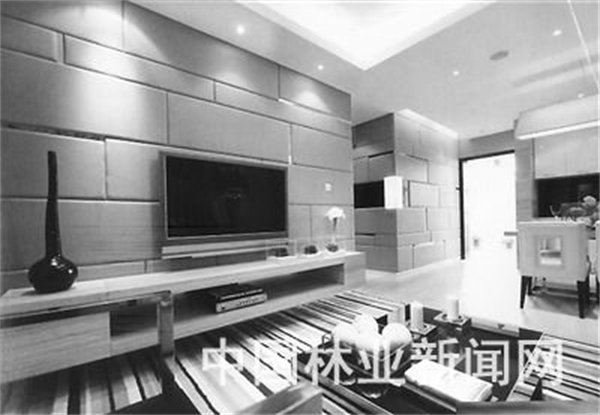
Yanli's "Natural Plant Fiber Composite Panel" Achieves Zero Formaldehyde Technology
The research and development of "natural plant fiber composite materials" to achieve zero formaldehyde technology is the hard work of Zhuang Ming, chairman of Jiangyin Yanli New Materials Technology Co., Ltd. in recent years. Jiangyin Yanli New Materials Technology Co., Ltd. is affiliated to Jiangyin Yanli Automotive Trim Co., Ltd. (hereinafter referred to as "Jiangyin Yanli"). Jiangyin Yanli was founded in 1996. After rapid development in recent years, it has achieved specialized production and has formed a series of products such as natural plant fiber composite panels, automotive interior and exterior trims, rail train interior trims, and new wall panels for green buildings. It is well-known in the industry for its technological innovation and modern management.
Zhuang Ming introduced to reporters that Yanli Company took the lead in establishing a provincial natural plant fiber composite material engineering technology research center in the industry, and after 6 years, it jointly developed a natural plant fiber composite material with the Chinese Academy of Forestry. The material uses natural hemp fiber and food-grade PP fiber as raw materials. After glue-free bonding technology, it is pressed and formed by a thermoplastic composite process at a high temperature of more than 200 degrees Celsius, realizing the formaldehyde-free characteristics of natural plant fiber composite boards, truly solving air pollution from the source of basic materials, and conforming to the development trend of energy conservation and environmental protection. It is reported that the natural hemp fiber composite board has obtained the China Environmental Labeling Product Certification Certificate issued by the Ministry of Environment and Ecology in February 2018. "We want to lead a milestone change in the decoration industry and become the first in the application of natural fiber composite products!" said Zhuang Ming.
It is reported that hemp fiber is a high-strength, low-stretch fiber with a breaking strength of 5.0-7.0 cN/dtex. Therefore, hemp fiber is relatively hard and does not easily deform. The development of ecological hemp fiber composite integrated decorative panels is the most direct way to reduce the amount of log products, and it also has the effect of enhancing material performance. It can be widely used in architectural decoration, automotive interiors, rail train interiors, cruise ship interiors and other decorative materials. At the same time, hemp fiber composite panels have better sound absorption, heat insulation and flame retardant properties, and are a new star in green building decoration materials.
Zhuang Ming told reporters that in the hemp fiber composite panels produced by Yanli, hemp fiber raw materials account for up to 70%. Hemp fiber composite panels are not only environmentally friendly, but also degradable and renewable. They are an environmentally friendly biomass composite material. Under the development theme of energy saving, low carbon and ecological environmental protection in the panel industry, hemp fiber composite panels have good development prospects.
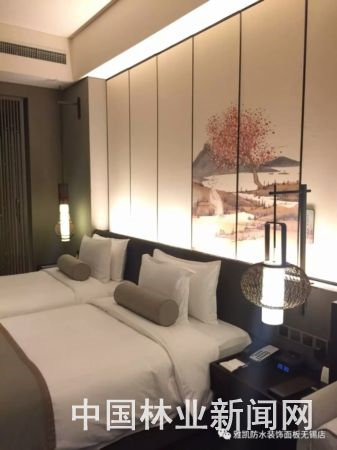
Hundreds of boats are competing to gallop on the road of high-tech
For Zhuang Ming, since the establishment of Jiangyin Yanli in 1996, he has always adhered to the route of scientific and technological innovation. "He himself is a person who likes to do research," said another person in charge of the company during the interview. In Zhuang Ming's words, Yanli is "to 'gather the wisdom of experts from all over the world, create 'New in science and technology', innovation has shaped the infinite charm of enterprises, and innovation is the eternal theme of enterprise development. ”
In addition to being the first in the industry to establish the Jiangsu Province (Yanli) Natural Plant Fiber Composite Materials Engineering Technology Research Center, Jiangyin Yanli has also carried out long-term industry-university-research cooperation with the Institute of Wood Industry of the Chinese Academy of Forestry, Jiangsu University of Science and Technology, Nanjing Normal University, etc.; the company has an academician workstation, and in 2014 signed an industry-university-research cooperation agreement with Nanjing Forestry University. Zhang Qisheng, an academician of the Chinese Academy of Engineering, organized an academician team to jointly tackle key problems around the research and development of environmentally safe new high-performance biomass composite engineering materials, realize the industrialization of results, and improve the company's innovation ability.
The reporter saw various honorary certificates and patent certificates displayed in the cabinet in the company's conference room. Zhuang Ming told reporters that after technical breakthroughs, the company has developed lightweight and high-strength new composite materials for interior decoration, thermoplastic natural hemp fiber composite substrates, hamburger-style hemp fiber boards, lightweight environmentally friendly hemp fiber composite boards, natural plant fiber composite rail train floors and other products, and has obtained 15 authorized patents, including 7 invention patents, and won honors such as the key new product certificate and the Jiangsu Province High-tech Product Certificate.
In the production workshop of Jiangyin Yanli, the reporter saw workers producing hemp fiber composite boards, and there was a complete set of automated production lines in the workshop. It is reported that this is the equipment production line that the company spent more than 20 million yuan to import from Italy last year. "Jiangyin Yanli currently has an annual production capacity of more than 5 million square meters," Zhuang Ming introduced. The standardized factory buildings and international automated production equipment ensure the modern production of products. At the same time, the core technology of environmentally friendly hemp fiber composite molding brings the company sufficient market confidence.
Looking to the future, Zhuang Ming is full of confidence, "We don't have to do , but we must do . We use the concept of green and environmental protection to serve the public, let green and environmentally friendly products based on natural fiber composite materials enter thousands of households, and make people's lives more low-carbon and healthier. We will strive for the environmental protection and ecologicalization of interior materials across the country, starting with the Jiangyin 'Easy Home Tiancheng' brand."